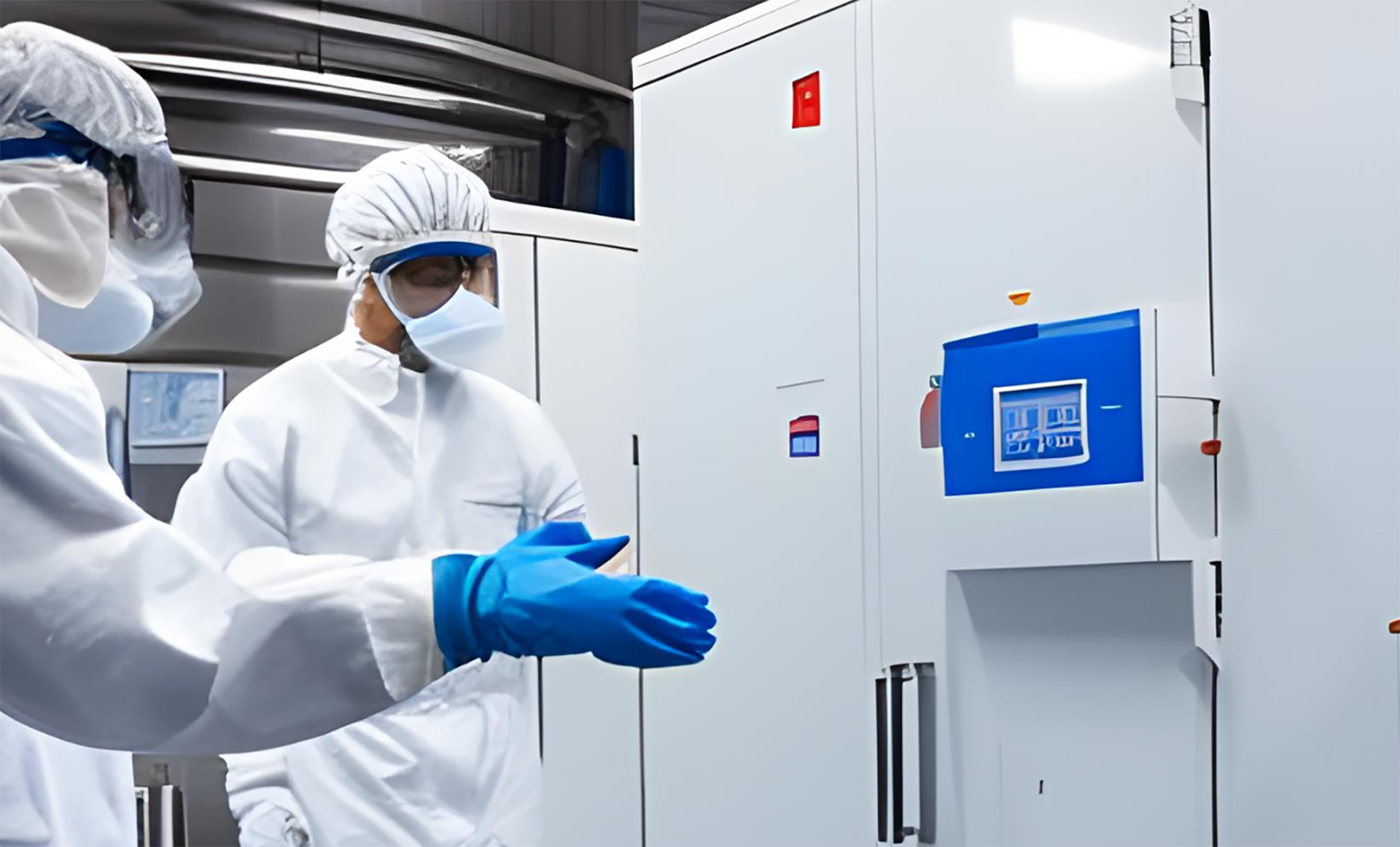
It’s a scenario that’s been played out for decades; someone or some group makes an error, and the manufacturing process comes to a halt, or worse, a lot is terminated. Cue human nature. Find someone to blame. The deviation is labeled as human error, followed by either a retraining or document update CAPA, and case closed. This is where the industry needs to evolve and start thinking differently about human error. These events are gold mines of information that will aid in developing ideal CAPAs. Asking a few simple questions, as soon as possible after the event, can help you uncover so much about cultural norms, behaviors, and how well your people are prepared for their role, understand the expected outcome of each step, and are supported during the process.
Human error events are typically stressful, and they often bring about feelings of shame or guilt for those involved. If left unchecked, this can lead to altered memory or a continuation of errors. As a result, it is important to pause and take a moment to regroup after an event occurs. During this time, information about the event can be uncovered that will greatly improve the investigation closure timing and if required, the development of an appropriate CAPA. The area management and individual(s) involved should walk through these five questions together, with the manager taking the lead. Findings should be shared with the team, and cross-functionally, to help prevent the same types of errors.
- What happened?
a. These are the basic facts. Include information about the who and when, making note of procedures, equipment, or other materials associated with the event. It is also important to understand where the process currently stands, and what actions may need to be taken immediately to regain positive control. - What was supposed to happen?
a. Have the individual(s) give you this information in their own words, and ask further probing questions if needed, such as:
i. What were the expected actions required by the batch record, procedure, or other guidance document?
ii. Are instructions clear?
iii. Was the guidance document available and appropriate revision used?
vi. How is the task verified as accurate and complete? - Why did this event happen?
Ensure the individual(s) knows they are safe to be open and transparent about the error. This should include any error traps they may have experienced, such as distractions in their work environment, lack of proficiency, inaccurate risk perceptions, or interpretation discrepancies regarding the task. Were there unclear goals or responsibilities? Was someone operating from a complacent or over-confident mindset? Or was the individual on autopilot, performing continuous repetitive actions? Try to remember people do not choose to err, so this is the best time to practice putting oneself in someone else’s shoes. What specific actions or behaviors led to the error? Understanding the sequence of actions or behaviors that led to the error is essential for identifying the immediate cause. This question focuses on the specific actions performed by the individual or individuals involved in the incident. - How can we prevent this error from recurring?
- What lessons can be shared?
a. These questions help empower the individual(s) involved in the human error event. They are the closest to the error and likely have good ideas to prevent it from happening again. It also helps them reframe the error into something positive, formulating lessons learned that can be shared with their team, so others don’t make the same error. This is so important for our brains, because when we know what can go wrong, we are better at recognizing and recovering.
By asking these questions after a human error event occurs, you can gain a comprehensive understanding of the root cause and implement effective corrective actions to prevent similar incidents from occurring again. In the next blog post, I will break down the three different types of human error and the corrective and preventative actions you can take to prevent them.
Sarah Boynton, a Consultant on the Quality Executive Partners team, has extensive experience in the biopharmaceutical/cell and gene therapy space, with a particular focus on cGMP training, human performance/error prevention, downstream processing, and non-conformance investigations. Prior to joining QxP, Sarah worked for Catalent Pharma Solutions, KBI Biopharma, AstraZeneca, Med Immune, and GlaxoSmithKline.