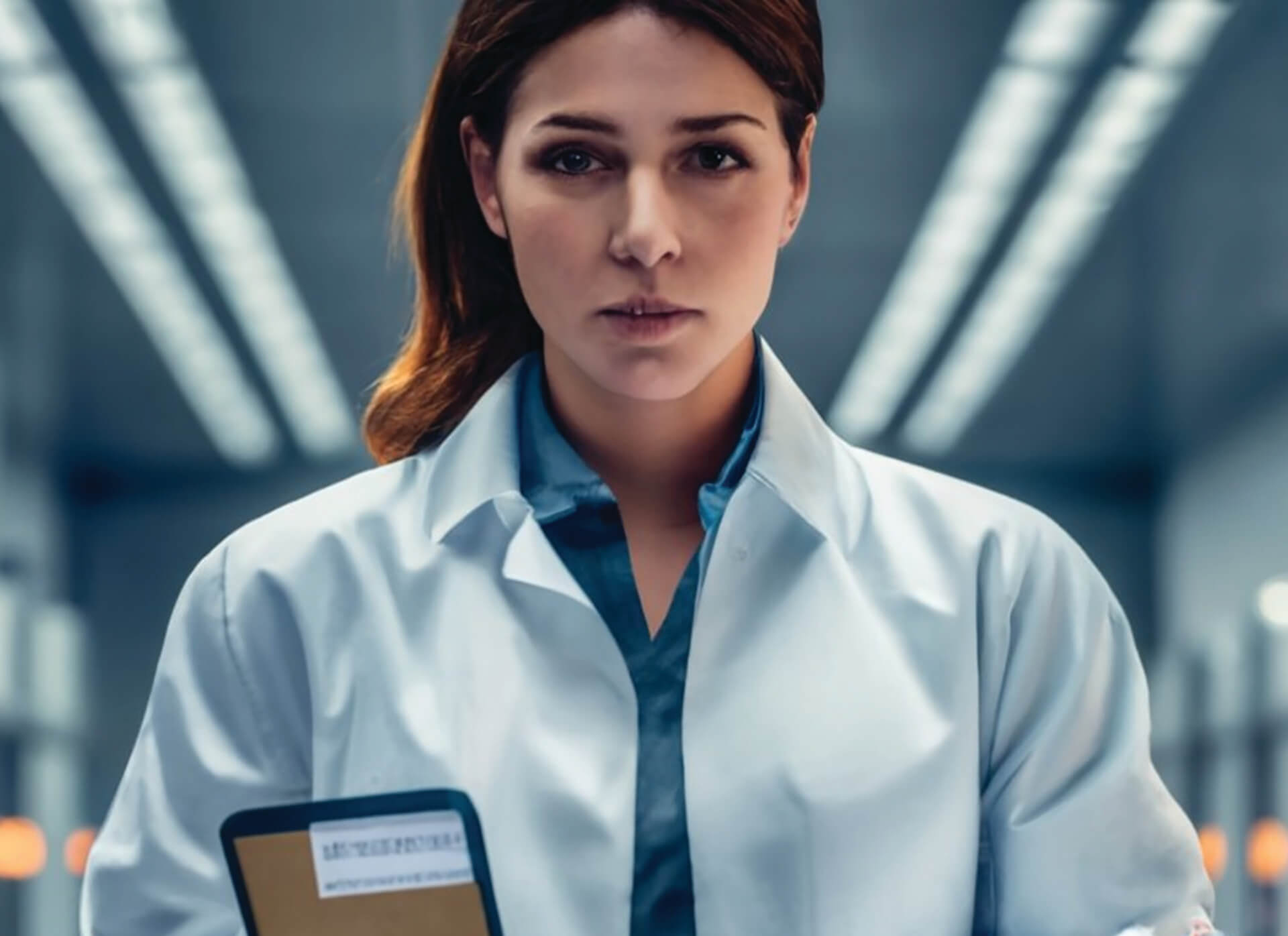
Let’s be honest—no one jumps for joy at the thought of a deviation. But, as seasoned professionals, we know that deviations are not just roadblocks; they're opportunities for improvement and learning. The "why" behind conducting a thorough investigation is simple: to understand the root cause, to prevent recurrence, and to continuously improve the quality of our operations.
Why is this so important? Well, a poorly conducted investigation is like putting a band-aid on a bullet wound—it might cover the problem temporarily, but it doesn't solve the underlying issue. A well-executed deviation investigation, on the other hand, provides invaluable insights that can be integrated into future operations through corrective and preventative actions.
Whether you're a seasoned veteran or a newcomer eager to learn, here are 4 best practices for performing effective investigations.
- Prompt and Thorough Documentation: It is essential to document any and all information associated with an event. These relevant details include things like date, time, location, personnel involved, equipment involved, ongoing activities and the documents or procedures being used, and a clear description of the event. One way to foster this is through a deviation capture form that can be accessed and completed quickly by those involved in the event. Perhaps part of the process is also to have Quality or management involved in taking interview statements while the memory is still fresh. Comprehensive documentation serves as a foundation for the investigation process and helps in identifying the root cause and implementing appropriate corrective actions.
- Robust Root Cause Analysis (RCA): If it is not immediately clear as to the root cause of the deviation, a formal root cause analysis should be performed. Work as a team to utilize appropriate tools and techniques, such as the 5 Whys, Fishbone (Ishikawa) diagram, or Failure Mode and Effects Analysis (FMEA), to systematically explore potential causes. Involving cross-functional teams, including subject matter experts or clients, helps to gain different perspectives and insights. This collaborative approach enhances the quality and comprehensiveness of the investigation.
- Data Collection and Analysis: Collect relevant data and analyze it systematically. This includes examining batch records, process parameters, environmental conditions, equipment logs, and any other data points that may be pertinent to the deviation. Analyzing the data can help identify patterns, correlations, and trends, providing valuable insights into the deviation's root cause. Utilize statistical tools and trending analysis techniques to make data-driven decisions. Make sure part of the data collection includes thoughts from those involved as to what environmental or behavioral changes would prevent the deviation from happening again.
- Sharing Information: Sharing this data and information gathered during the course of a deviation investigation sets high-quality organizations apart from others. Often times the event or failure can happen in other departments or on other teams, and in an effort to reduce metrics, the wealth of information garnered during the investigation gets forgotten. Frequently reviewing and sharing the contents of a deviation investigation will help raise awareness and prevent recurrences.
Always remember, foster an open and blame-free environment where all stakeholders can share information and contribute their expertise. Continuous improvement should be the ultimate goal, ensuring that the lessons learned from the investigation are incorporated into future processes to prevent similar events from occurring.
Sarah Boynton, a Consultant on the Quality Executive Partners team, has extensive experience in the biopharmaceutical/cell and gene therapy space, with a particular focus on cGMP training, human performance/error prevention, downstream processing, and non-conformance investigations. Prior to joining QxP, Sarah worked for Catalent Pharma Solutions, KBI Biopharma, AstraZeneca, MedImmune, and GlaxoSmithKline.
Check out Sarah’s recent blog: “The Art of Viral Vector Manufacturing: 4 Essential Controls to Prevent Cross-Contamination.”