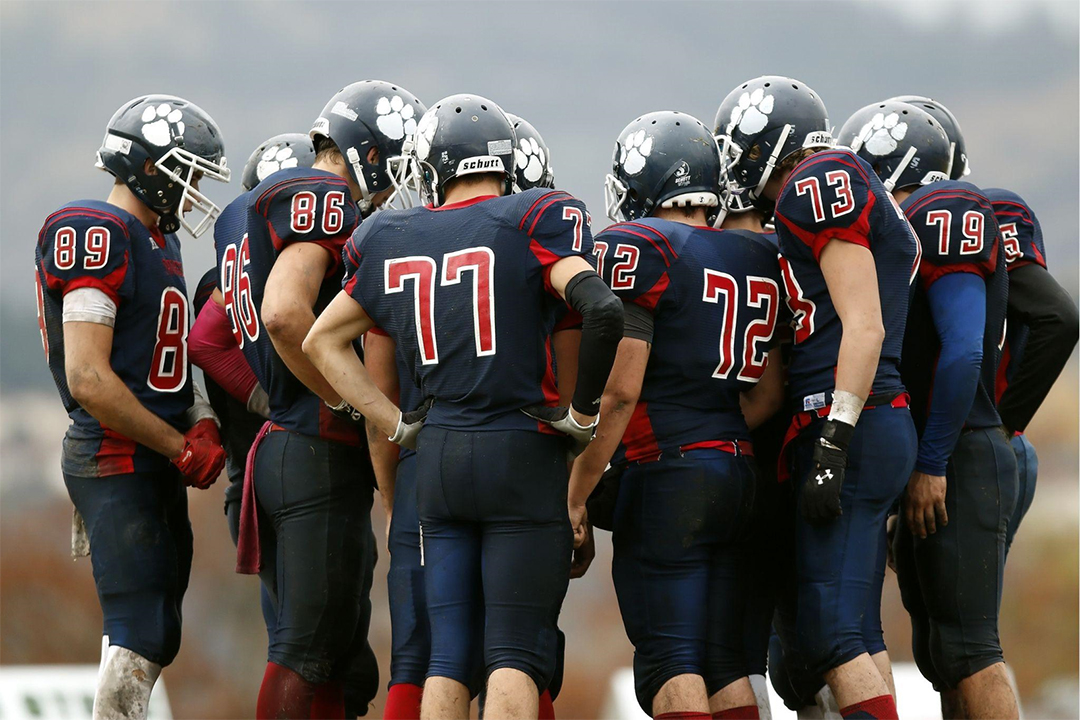
Has our industry lost its way when it comes to product quality? Our quality units seem to be focusing on reviewing documents and assembling metrics. Most, if not all, of these activities focus on the rearview mirror, catching errors in batch records, investigating deviations, and monitoring how long it takes to get the deficiencies in the manufacturing process corrected so we can release product. What is wrong with this picture?
Have we forgotten that quality must be built into what we produce? We seem, as an industry, to have figured out how to maintain a safe working environment, probably learned from other industries, where we identify the risks inherent in our daily workplace, and either engineer them out or teach our workers how to avoid the danger. We also, in many cases, establish safety cultures that include regular safety audits and programs to remind everyone how to avoid risks. We then use one or two simple metrics to monitor and celebrate our success.
In pharmaceutical and biopharmaceutical manufacturing today, we seem to prioritize speed and cost control in the manufacturing supply chain, but don’t seem to understand that building in quality will contribute significantly to both metrics. Where, then, do we refocus our quality resources to have an impact on quality before and during production, where right the first time becomes the simple, most important metric of quality product?
1. Process design and validation – Quality units should be establishing a role to partner with scientists and engineers to ensure the process design is robust, well-tested, and proven capable through a strong validation exercise. This is accomplished by partnering in the development and execution, not limiting quality involvement to review and comment after the fact.
2. Effective Instructions – Regardless of title, batch record, work instruction, or checklist, whenever humans are involved, the ability to easily understand and follow what and how a task is accomplished must be provided and available during the manufacturing process.
3. Sufficient Education and Training – Providing dozens of standard operating procedures and asking someone to simply read and understand, coupled with a few days watching someone else perform a task, is a recipe our industry has followed for decades, and the consistently poor results are reflected in the unchanging regulatory deficiencies seen by our colleagues in the FDA and other regulatory bodies. People learn by doing, developing the mental and muscle memory of how to perform tasks and achieving consistent and sustainable performance when they couple that with understanding the “why” behind performing the task.
4. Ongoing Coaching and Positive Reinforcement – As organizations have chased cost controls, the role of supervision has evolved into one of administration of documentation, both in operating and quality units. The definition of supervision is “a critical watching and directing of activities or a course of action.” As an industry, we must allow supervisors and quality experts on the floor to fulfill this role. This, of course, means investing in these individuals so they have the expertise to properly coach and mentor operators.
If you agree with me that these four areas of focus are the true foundation for quality pharmaceutical and biopharmaceutical manufacturing, how do we start the transition?
I believe it must start with a cultural shift in leadership, from maintaining compliance to building quality into the process. Quality leaders must build both an organizational structure and skill level in their teams to proactively participate and lead in these four key quality elements. Quality, as we have done with safety, must be primarily a proactive, preventive effort with the retrospective activities like document review and deviation management relegated to a subordinate role supporting continuous improvement.
We must protect our patients in the same manner as we protect our workers. Quality is definitely not a spectator sport!
________________________________________________________________________
QxP Vice President Mike Levitt started his more than 30-year career in pharma leadership as Director of Production Operations at Eli Lilly and Company back in 1989.
Check out Mike’s other recent blogs: “Is it Time to Outsource Internal Auditing?” and “Six Keys for Effective Deviation Investigators.”