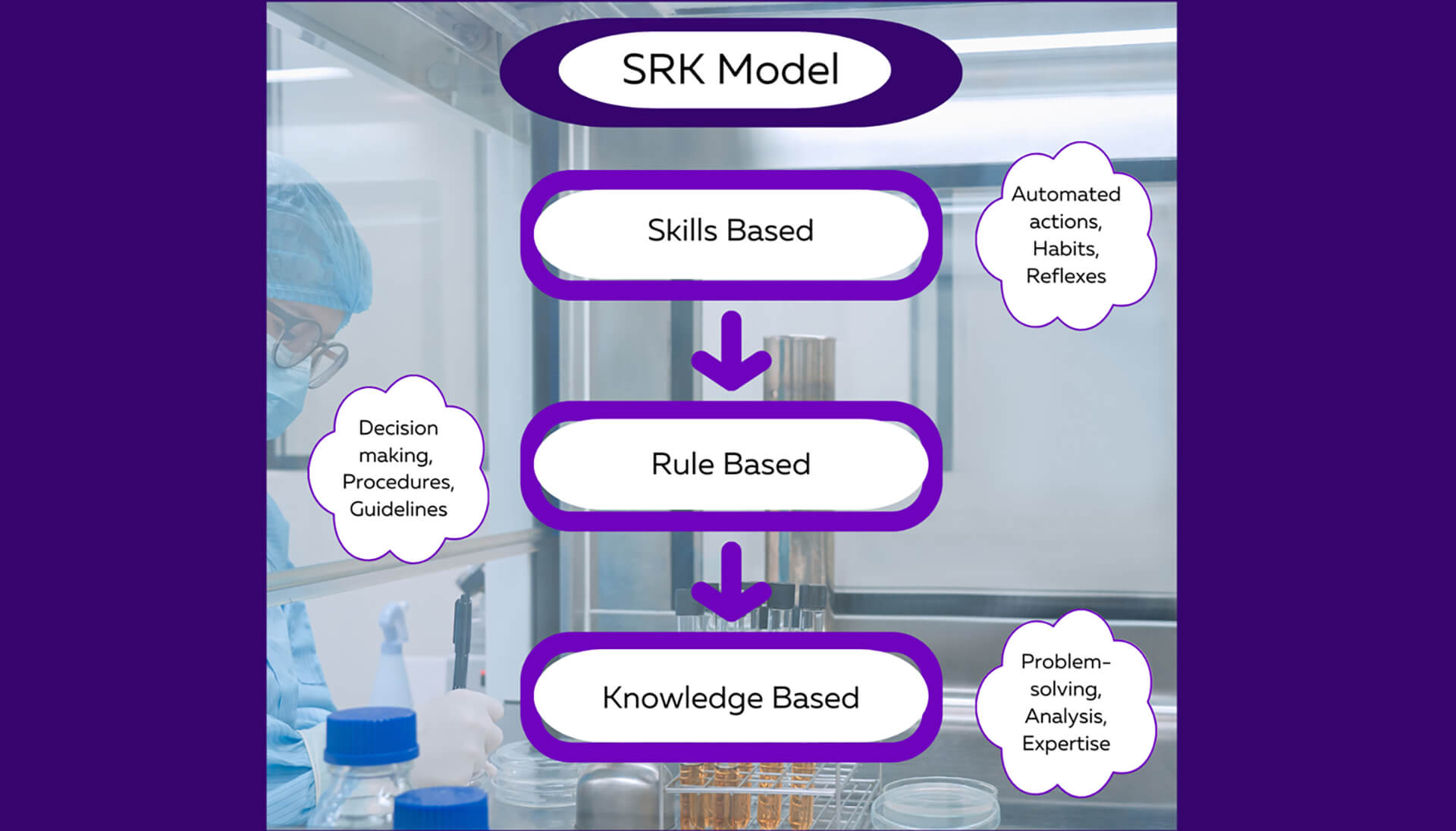
Human performance plays a crucial role in all aspects of our lives, ranging from everyday tasks to complex professional endeavors. However, even the most skilled individuals are prone to making errors. Understanding the different types of errors and implementing corrective actions can significantly enhance performance and minimize mistakes. In this blog post, we will delve into the three main types of errors: slips, lapses, and mistakes, and explore effective strategies to address each of them.
As we examine the intricacies of human performance and the different types of errors, it becomes clear that a comprehensive approach is required to unlock our full potential. Thankfully, the cognitive scientist Jens Rasmussen's did this for us with his SRK (Skills Based, Rule Based, and Knowledge Based) model. The SRK model offers valuable insights into the underlying mechanisms of human performance and how errors manifest in various contexts. Rasmussen's work emphasized that as individuals acquire expertise in a particular domain, their actions progress through three levels: skills-based, rule-based, and knowledge-based. Slips and lapses primarily occur at the skills-based level, where automated and habitual actions take place. These errors often arise due to momentary distractions or deviations from established routines. Think of being on autopilot. Mistakes, on the other hand, are more likely to occur at the rule-based and knowledge-based levels. They involve conscious decision-making and may stem from faulty assumptions, inadequate knowledge, or flawed reasoning. In these levels, individuals are integrating, interpreting, and applying what they’ve learned or experienced. By incorporating Rasmussen's insights into the SRK model, you can gain a deeper understanding of the cognitive processes underlying slips, lapses, and mistakes. This awareness enables you to tailor CAPAs accordingly, fostering a holistic approach to error prevention and performance improvement.
- Slips: Slips are unintentional actions that result in an unintended outcome. The keyword here is “unintentional.” We have to remember that people do not go to work thinking, “today I am going to mess up!” Slips typically occur when a person's performance deviates from their intentions due to a momentary lapse inattention or an automatic response. Slips can be categorized as motor or cognitive slips. For example:
- A QC technician accidentally selects the wrong reagent or solution due to similar labeling or packaging,
- Or transfers an incorrect volume of a substance during a pipetting process due to momentary distraction,
- An operator mishandles a piece of equipment, leading to unintended contamination or spills.
a. Potential CAPAs:
i. Increase awareness: Being mindful of one's actions and maintaining focus can reduce the occurrence of slips. Taking a moment to pause, breathe, and concentrate on the task at hand helps prevent distractions. A great tool here is the STAR tool: Stop, Think, Act, Review
ii. b) Implement reminders and checklists: Utilizing reminders, checklists, or visual cues can help individuals stay on track and avoid slipping into automatic modes of behavior. These aids serve as external prompts and keep important details at the forefront of one's mind.
iii. c) Improve ergonomics and design: Optimizing the environment and workflow can minimize slips. Simple modifications such as arranging tools and equipment for easy access, reducing clutter, and designing intuitive interfaces can enhance performance and reduce the likelihood of errors. - Lapses: Lapses are errors of omission, where an individual forgets to perform a necessary action or fails to complete a task. They often occur due to a lack of attention, memory failure, or absent-mindedness. For example:
- An operator forgets to document a critical step or measurement,
- Or neglects to open their SOP because they’ve done the task a million times and skips a necessary quality control check,
- A QA release technician overlooks the expiration date of a crucial reagent or material, leading to the release of outdated components.
Like slips, lapses occur during actions that require little conscious control. Typically, individuals who experience slips and lapses are extremely experienced with the task and because of this, re-training is never the answer..
a. Potential CAPAs
i. Utilize reminders and alarms: Employing technology, such as setting reminders on smartphones or using alarm systems, can help counteract memory lapses. These tools provide timely prompts and ensure critical tasks are not overlooked.
ii. Establish routines: Establishing consistent routines and habits helps minimize lapses by transforming important actions into automatic behaviors. By performing tasks regularly at specific times or following a predetermined sequence, individual scan reduce the risk of omission. GDP errors often are the result of a slip or lapse, so establishing real-time or frequent document review during a shift will help with recognition of these errors.
iii. Enhance working memory: Techniques such as mnemonic devices, visualization, and association can aid in remembering important information. Breaking complex tasks into smaller, manageable chunks and actively rehearsing key details can improve memory retention. - Mistakes: Mistakes differ from slips and lapses as they involve a conscious decision-making process that leads to an incorrect or undesirable outcome. Mistakes often arise due to flawed reasoning, incorrect assumptions, or inadequate knowledge. When individuals make a mistake, there is almost always some form of problem solving that needs to occur. They typically thought they were doing what they were supposed to, but their planning was flawed. Any shortcomings in an individual’s knowledge or their limitations in applying existing knowledge to new situations will be evident. For example:
- An operator misinterprets the data analysis results and makes decisions based on flawed interpretations, leading to incorrect adjustments in manufacturing processes,
- Engineering qualifies a bioreactor with incorrect specifications, resulting in suboptimal growth conditions for the cells or microorganisms,
- Quality and Manufacturing management fail to adequately assess potential risks associated with a new manufacturing processor technology, leading to unforeseen safety or quality issues.
a. Potential CAPAs
i. Continuous learning and training: To reduce mistakes, individuals must invest in ongoing learning and professional development. Expanding knowledge, staying updated on relevant information, and seeking feedback from peers or mentors can enhance decision-making abilities.
ii. Encourage a culture of double-checking: Instilling a habit of verifying one's work and seeking second opinions can catch potential mistakes before they cause significant harm. This practice fosters a collective responsibility for quality assurance and encourages critical thinking.
iii. Foster open communication: Creating an environment where individuals feel comfortable discussing concerns and asking questions is crucial. Encouraging open dialogue and promoting a blame-free culture fosters collaborative problem-solving and minimizes the likelihood of mistakes going unnoticed. After action reviews are an amazing tool used by the military and many other high-risk industries, where an open dialogue between team members can help uncover what was supposed to happen, what actually occurred, what went well and why, and where improvement scan be made.
Understanding the various types of errors and implementing corrective actions is essential for optimizing human performance. By recognizing slips, lapses, and mistakes, individuals can take proactive measures to mitigate their impact. Cultivating mindfulness, utilizing reminders, establishing routines, continuously learning, and fostering open communication are key strategies to enhance performance and reduce errors. By incorporating these practices in to our daily lives, we can strive for excellence in our personal and professional endeavors.
Sarah Boynton, a Consultant on the Quality Executive Partners team, has extensive experience in the biopharmaceutical/cell and gene therapy space, with a particular focus on cGMP training, human performance/error prevention, downstream processing, and non-conformance investigations. Prior to joining QxP, Sarah worked for Catalent Pharma Solutions, KBI Biopharma, AstraZeneca, MedImmune, and GlaxoSmithKline.