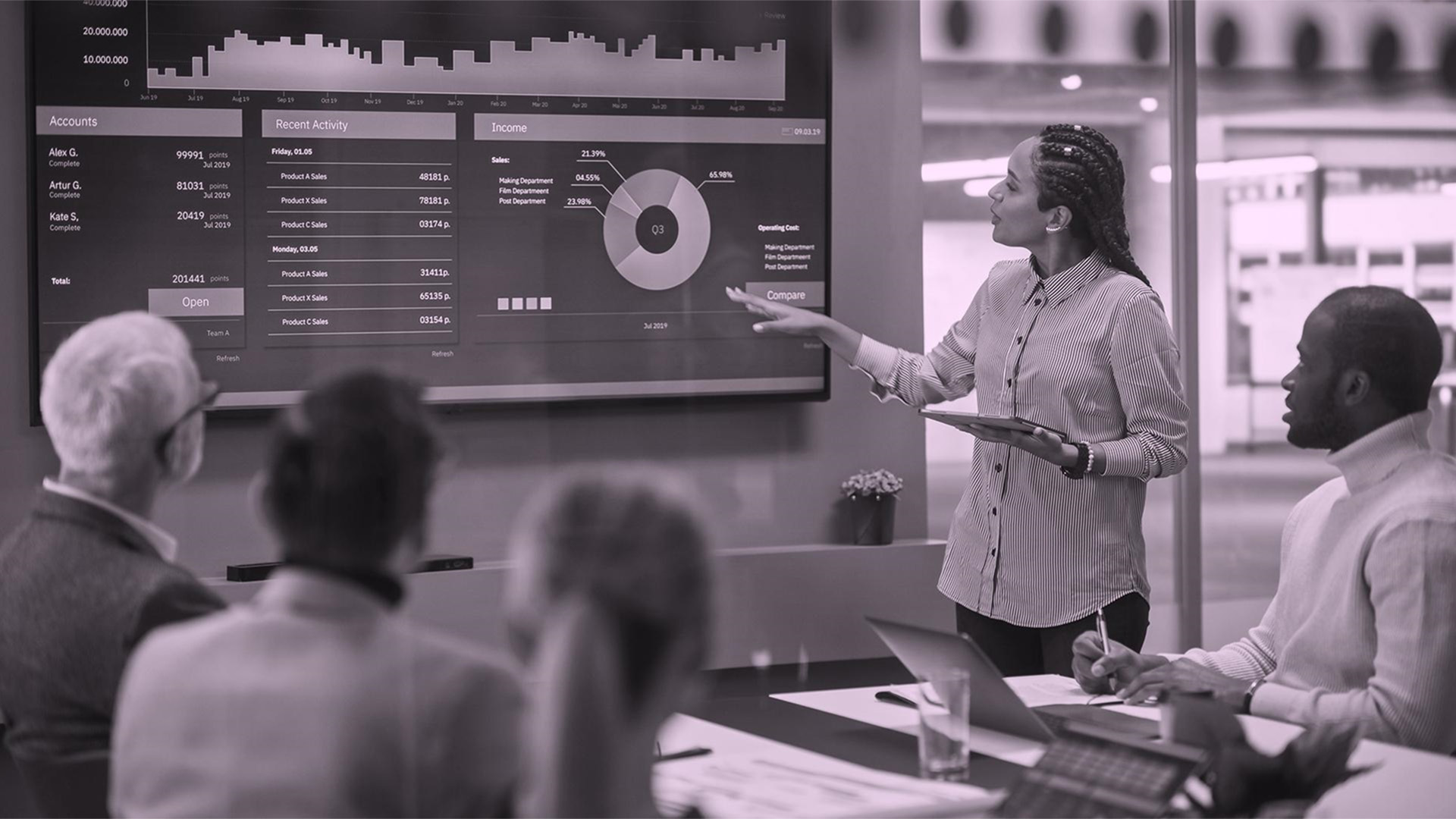
At the recent 47th annual International GMP Conference in Athens, Georgia, I discussed the fact that the objective of internal auditing is to self-identify opportunities for improvement.
For the quality side of operations, the goal is to ensure that quality systems are properly designed and functioning as intended. I have been asked by senior leaders in some organizations, “If I have an internal auditing team and procedure, why am I still receiving observations during regulatory audits?” The answer is complex and depends on both the internal environment of the company and the external business environment in which it is operating.
The fundamentals for having an effective internal auditing program really haven’t changed since the practice was developed in the early 1940s as companies rapidly grew to meet the production demands for materials during the second world war. It begins with senior leadership being committed to quality and compliance, prioritizing remediation of any findings. It requires a program with clear objectives and procedures designed to assess and correct, if necessary, any aspects of the quality system that may compromise product quality or regulatory compliance.
Finally, a successful program requires auditors who have the technical expertise to objectively evaluate the system coupled with the skills to communicate effectively up and down the organization what changes are required. Without all these factors in place, a company’s internal auditing program quickly becomes a bureaucratic exercise consuming significant resources but yielding little benefit.
In today’s pharmaceutical manufacturing industry, changes both in rapidly advancing technologies and in the general work culture are driving the need to alter our approach to internal auditing.
The rapid growth of biopharmaceuticals coupled with the accelerating trend to utilize third parties to manufacture clinical and commercial materials are redefining what ‘internal auditing’ needs to achieve.
Further, the landscape of work culture is changing. Many new and smaller start-up companies are often populated by less experienced staff and have much higher turnover rates. This contrasts an era when only large multinational pharmaceutical companies dominated the development and manufacturing of medicines. This tendency toward staff churn is undermining the effectiveness of internal auditing to help ensure self-regulation of quality and compliance.
The incredible advances in new therapies and vaccines to treat and cure diseases require innovative, ‘out of the box’ thinking. This revolution also demands new approaches to internal auditing. We need to redefine approaches in ways that allow the process to achieve quality and compliance in this shifting landscape.
In this environment where companies have limited internal resources and outsource manufacturing to third parties, should we follow the same path developed more than 80 years ago? Or should companies turn to third-party resources to provide objective subject matter experts to periodically conduct audits covering internal quality systems and the quality/compliance relationship with external manufacturing partners?
Recent FDA inspection data shows that the major observational trends have not changed significantly in the last 20 years, so internal auditing in its current form has not proven effective in driving needed change.
An effective internal auditing program is but one critical element in maintaining product quality and the impact can only be seen over time in a consistent and well-run program. A change in how we conduct internal auditing is needed, outsourcing for some may be the answer.
QxP Vice President Mike Levitt started his more than 30-year career in pharma leadership as Director of Production Operations at Eli Lilly and Company back in 1989.