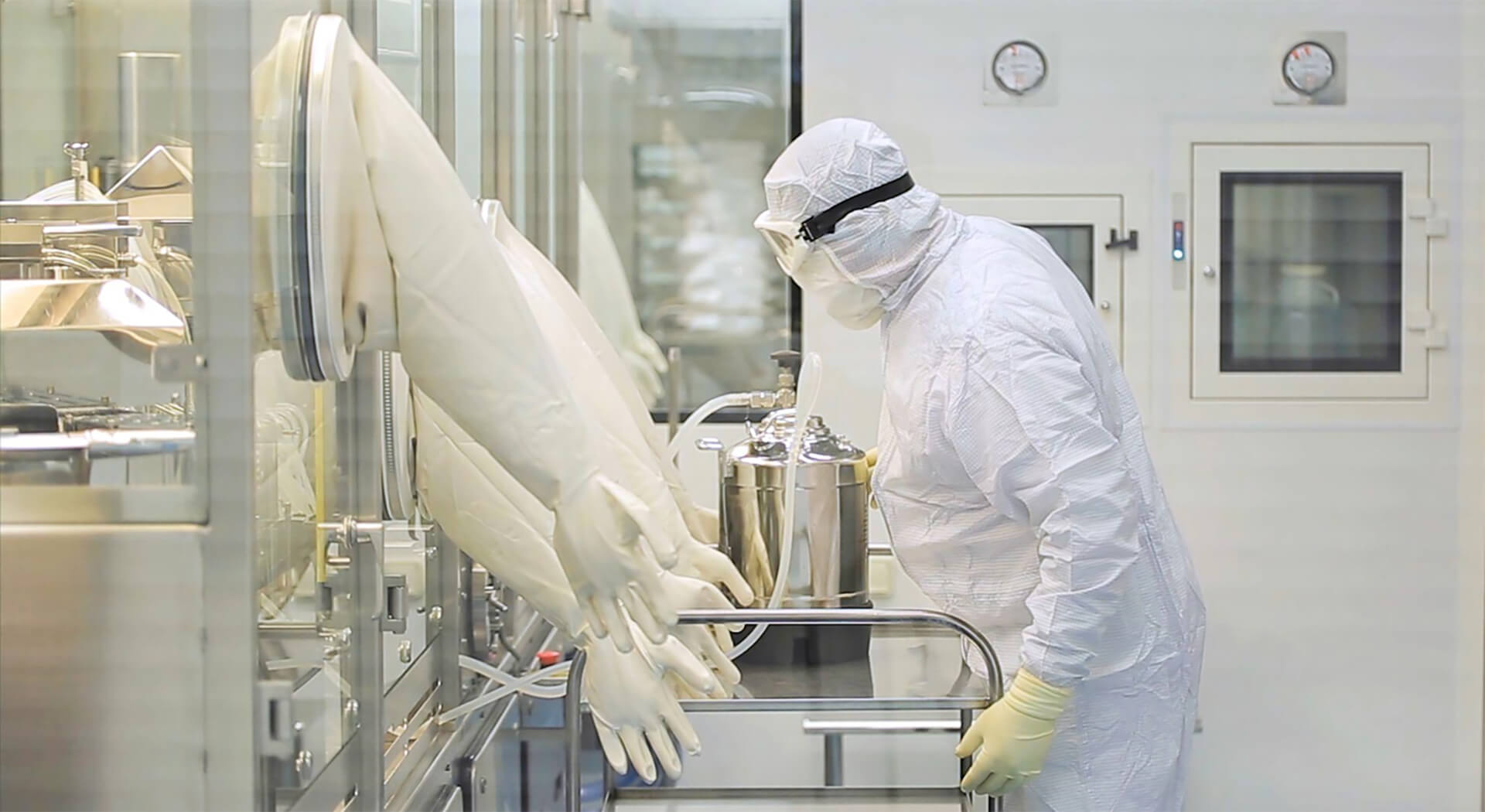
In the world of cGMP manufacturing, where precision and accuracy are paramount, preventing human errors is crucial to ensure product quality, regulatory compliance, and the safety of both patients and employees. To mitigate the risk of human errors, manufacturing facilities can employ various tools and strategies. In this blog post, we will explore three essential human error prevention tools and discuss how they can be effectively used.
1. Pre-Job Briefing:
A pre-job briefing, or PJB, is a structured communication process that takes place before starting a task or activity. It involves gathering relevant personnel to discuss and review the specific requirements, potential risks, and critical steps involved in the job. Pre-job briefings serve as a powerful tool in preventing human errors by fostering clear communication, increasing situational awareness, and aligning the team's understanding of the task. This should be 5-10 min and can serve as your pre-shift huddle.
Using pre-job briefing effectively:
a. Team Collaboration: A pre-job briefing should involve all personnel who will be directly involved in the task, including technicians, operators, and supervisors. This ensures that everyone is on the same page, understands their roles, and can contribute their expertise and insights to the discussion.
b. Task Analysis and Risk Assessment: Before the briefing, a thorough task analysis should be conducted to identify potential risks and hazards associated with the job. What could go wrong? Who should be notified? This analysis helps in identifying critical steps, potential sources of errors, and appropriate preventive measures. During the briefing, the identified risks should be discussed, and strategies for mitigating them should be determined.
c. Clear Communication and Confirmation: The pre-job briefing should provide a platform for open communication, where participants can ask questions, seek clarification, and share concerns. It is essential to encourage active engagement and ensure that everyone understands the task requirements, safety precautions, and any special considerations. The team should confirm their understanding of the discussed information, and any necessary adjustments or additional instructions should be provided. Try switching up who leads the PJB each week and for a gold star, generate a weekly report identifying important discussions and items identified during these sessions.
2. Error-Proofing Techniques (Poka-Yoke):
Error-proofing techniques, often referred to as Poka-Yoke (a Japanese term meaning "mistake-proofing"), involve designing processes and systems in a way that makes errors or mistakes nearly impossible to occur or detect them before they result in a problem.
Implementing error-proofing techniques:
a. Visual Cues and Color Coding: Do you have shared cold rooms or kanban areas? What about sample receipt and storage locations? Incorporating visual cues, such as color-coding or using standardized labels, can help employees easily identify and differentiate between different materials, tools, or processes. This reduces the chances of errors due to incorrect selection or usage.
b. Foolproof Tools and Equipment: Designing tools and equipment with built-in features that prevent incorrect usage or assembly can significantly reduce human errors. For example, using connectors that can only be connected in one orientation eliminates the possibility of incorrect connections.
c. Automated Controls and Validation: Leveraging automation technologies and implementing built-in validation checks can minimize the risk of human errors. Automated controls can verify critical parameters, perform calculations, and flag any deviations or inconsistencies, reducing reliance on manual inputs and reducing the likelihood of errors.
3. After Action Review (AAR):
The AAR is a structured approach that allows teams to reflect on their performance after completing a task or project. It provides an opportunity to identify what went well, what could have been done better, and what lessons can be learned to prevent future errors.
Using AAR effectively:
a. Reflective Discussion: AAR sessions should involve all team members who participated in the task. Facilitate an open and honest discussion, allowing each team member to share their observations, insights, and recommendations. Focus on understanding the underlying causes of any errors or issues that occurred during the task.
b. Identify Lessons Learned: Encourage the team to identify specific lessons learned from the experience. This may include identifying process gaps, training needs, or improvements in communication and coordination. Document the lessons learned and share them with relevant stakeholders to drive continuous improvement.
c. Action Planning: Based on the insights gained from the AAR, develop an action plan to address the identified areas for improvement. Assign responsibilities and establish timelines to ensure that corrective actions are implemented effectively. Regularly review the progress and impact of the action plan to monitor the effectiveness of the improvements made.
Human errors in cGMP manufacturing can have severe consequences, ranging from compromised product quality to regulatory non-compliance and patient safety concerns. Employing the right tools and strategies is vital to prevent and minimize human errors. By implementing these human error prevention tools effectively, organizations can mitigate risks, enhance productivity, and ensure the delivery of safe and effective products to patients in need.
Sarah Boynton, a Consultant on the Quality Executive Partners team, has extensive experience in the biopharmaceutical/cell and gene therapy space, with a particular focus on cGMP training, human performance/error prevention, downstream processing, and non-conformance investigations. Prior to joining QxP, Sarah worked for Catalent Pharma Solutions, KBI Biopharma, AstraZeneca, MedImmune, and GlaxoSmithKline.
Check out Sarah’s other recent blogs: “The 5 Questions You Need to Ask After a Human Error Event Occurs” and “3 Types of Human Error and Potential CAPAs to Prevent Them.”