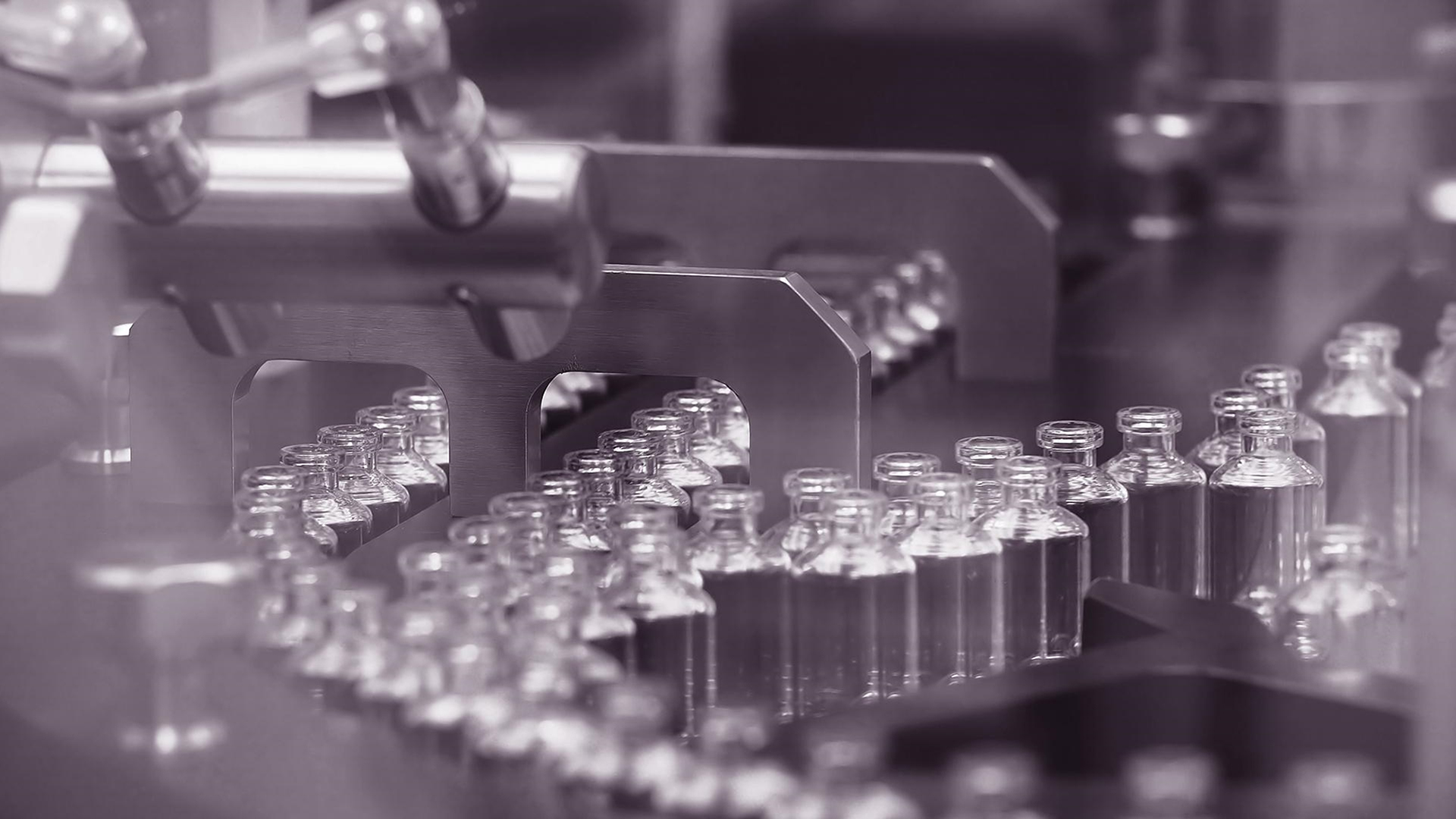
A Scenario to Consider
You just closed out a US FDA inspection. A Form 483 was issued and it covered what appeared to be a manageable list of observations. For your response, you plan to gather further information to explain every sub-bullet example more effectively. You’ll list the changes you plan to make within your procedures to ensure the issues are not repeated.
Let’s Take a Beat
Did you think to investigate the root causes of those failures (observations)? Was any time spent examining your operations and quality systems to see if there may be other related issues or similar problems elsewhere in your operation? These issues might play a bigger role than you imagine in impacting product quality and quality decision-making.
Upon Closer Examination . . .
You encounter a media fill failure upon finding multiple turbid vials. After a detailed review of the manufacturing and laboratory data, you identify several potential root causes, addressing each and repeating the Aseptic Process Simulation.
The repeat study ultimately meets specification requirements and commercial production is resumed. But, do you fully understand:
- Types of contamination found?
- Have you seen the substances before?
- Where were the substances introduced into your operation?
- How did the substances get there in the first place if your contamination control strategy and process controls were up to date?
Did you adequately consider the potential impact on previous batches produced wherein the same materials, production process, equipment, and personnel were used? How did those batches pass if less robust, routine release testing processes were employed?
It’s a Trap!
At a certain level, the initial actions described in both scenarios read, fundamentally as fully compliant approaches. However, you may have just fallen into a faulty compliance trap versus a quality mindset which is required to meet current industry and regulatory expectations.
The challenge here is the mindset that comes with how we think of the term “compliance” versus expectation. And where does quality fit in? All too often, being compliant is thought of as a means of achieving a requirement or standard. But how we apply that thought process is frequently far too narrowly applied in the immediate sense or scenario- intended to meet requirements or be compliant.
While the GMPs established during the 1960s provide the requirements, I think we can all agree the expectations today have expanded since. Shifting was demanded in response to new technologies, new insights, and occasionally an unfortunate crisis we have all learned from.
Learning and adapting is how we all remain vigilant against continuous and emerging threats that patients rely on us to control and avoid. If that’s the case, let’s offer a better focus.
Quality is a continuous improvement mindset; it ensures product quality expectations are consistently met, ultimately ensuring sustained compliance. This mindset, where compliance is an outcome, is only achieved through consistent and fully extensive application of the aforementioned quality mindset and by a well-educated and fully capable organization with a mature quality culture.
Avoid the compliance trap!
QxP COO Brian Duncan’s experience in pharma quality spans more than 20 years, including many years at Sandoz and Novartis prior to joining QxP.